In this article:
- Introduction
- The Basics of Vehicle Buses
- Unveiling the Controller Area Network (CAN Bus)
- The Message-Based Protocol
- Enhanced Noise Immunity
- Error Detection and Node Isolation
- Automatic Message Re-Transmission
- Variable Bit Rates
- A Glimpse into the Future: CAN Bus vs. RS-485
- Benefits of Utilising CAN Bus
- Overview of Key CAN Bus Applications
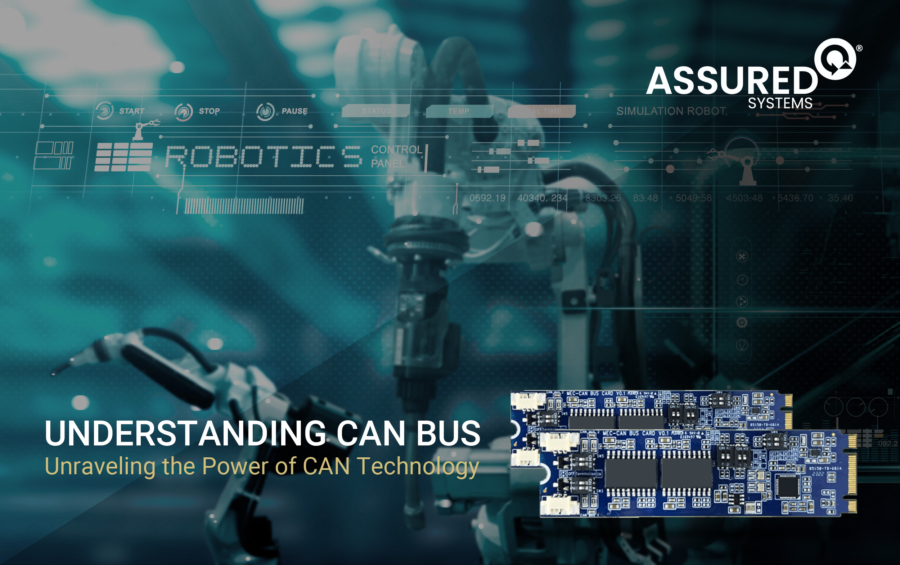
Introduction
In the ever-evolving landscape of such like automotive technology, communication is the key that unlocks the potential for innovation. Imagine a symphony of interconnected components within a vehicle, seamlessly working in harmony to ensure a smooth and safe driving experience. This interconnectedness is made possible through a complex network known as a vehicle bus, often referred to simply as a bus. Among the various types of vehicle buses, the Controller Area Network (CAN Bus) is used predominantly within automotive and industrial applications, standing as a unique and powerful communication technology that plays a pivotal role in modern vehicles.
The Basics of Vehicle Buses
To embark on our journey into the realm of CAN technology, we must first understand the foundational concept of a vehicle bus. Simply put, a vehicle bus is an internal communication network that connects various components within an automobile. These components, often referred to as electronic control units (ECUs) or nodes, encompass a wide array of functions, from engine management to climate control and safety systems. What makes vehicle buses indispensable is their ability to enable these ECUs to communicate directly with each other, all without relying on a central computer.
Unveiling the Controller Area Network (CAN Bus)
Now, let’s delve into the heart of this communication marvel – the Controller Area Network, or CAN Bus. It is an exceptional type of bus technology that has revolutionised the way electronic control units, especially within vehicles, interact with one another. Unlike traditional methods that necessitate a central computer to mediate communication, CAN Bus empowers nodes to communicate directly, making it a true peer-to-peer network.
The Message-Based Protocol
The effectiveness of the CAN Bus lies in its message-based protocol. This approach involves each message sent by a node carrying a unique identifier that predefines its priority. This system allows nodes to assess the importance of each message, ensuring efficient and streamlined communication. The result is a dynamic network where critical information can be prioritised and delivered swiftly.
Enhanced Noise Immunity
One of the distinguishing features of CAN Bus is its exceptional noise immunity. This characteristic is crucial in the context of an automobile, where a cacophony of electronic devices and electrical signals can introduce interference. CAN Bus tackles this issue through the use of differential signaling. In simple terms, it means that data is transmitted as voltage levels on two wires, and the receiver interprets the difference between these voltages. This setup allows CAN Bus to filter out external noise effectively, ensuring reliable and error-free communication.
Error Detection and Node Isolation
Within the automotive world, Safety is paramount and the CAN Bus system doesn’t disappoint. It boasts built-in error detection mechanisms that enable nodes to spot and report any anomalies in the data they receive. This functionality is pivotal in identifying potential issues and taking corrective measures promptly. Furthermore, the CAN Bus is designed with error node isolation, meaning that if one node malfunctions, it won’t disrupt the entire network. This redundancy ensures that the vehicle can continue to operate safely, even in the presence of a malfunctioning ECU.
Automatic Message Re-Transmission
In a system as critical as a vehicle’s communication network, errors are inevitable. However, what sets CAN Bus apart is its ability to rectify these errors efficiently. When an error is detected, the system automatically re-transmits the message, ensuring that no critical information is lost. This feature is instrumental in maintaining the reliability of the communication network, even in challenging conditions.
Variable Bit Rates
CAN Bus is a versatile technology that adapts to different requirements. During network initialisation, it allows for variable bit rates, meaning that the speed of communication can be adjusted to suit the specific needs of the nodes. This flexibility ensures that the network can efficiently handle a wide range of data transmission requirements, from high-speed sensor data to slower, but more critical safety-related messages.
A Glimpse into the Future: CAN Bus vs. RS-485
While CAN Bus shares some similarities with RS-485, it also possesses distinct differences that set it apart.
CAN (Controller Area Network) and RS-485 (Recommended Standard 485) are both serial communication protocols used in various applications, but they have some key differences. Here are the main differences between CAN Bus and RS-485:
- Network Topology:
- CAN Bus: Typically uses a multi-master, multi-drop topology, allowing multiple nodes to communicate on a single bus. It’s commonly used in automotive and industrial applications.
- RS-485: Supports a multi-point, half-duplex or full-duplex, point-to-point or multi-point topology. It’s used in a wide range of applications, including industrial automation and building control systems.
- Communication Speed:
- CAN Bus: Offers higher data transfer rates, typically ranging from 125 Kbps to 1 Mbps, making it suitable for high-speed applications like automotive and some industrial systems.
- RS-485: Generally has lower data rates, typically ranging from 9600 bps to 10 Mbps, making it suitable for applications with moderate to high-speed requirements.
- Data Collision Handling:
- CAN Bus: Implements a collision avoidance mechanism, allowing multiple nodes to transmit simultaneously without data corruption. This ensures a high level of reliability in data transmission.
- RS-485: Relies on the physical layer and external protocol mechanisms for collision avoidance. It does not have built-in collision detection and avoidance like CAN.
- Error Detection and Handling:
- CAN Bus: Offers built-in error detection and correction mechanisms, which contribute to its high level of reliability. It can detect errors and retransmit data automatically.
- RS-485: Lacks built-in error detection and correction. Error detection and retransmission must be handled at the application level if needed.
- Noise Immunity:
- CAN Bus: Designed for high noise immunity, making it suitable for automotive and industrial environments where electrical interference is common.
- RS-485: Provides good noise immunity but may require additional shielding and surge protection in noisy industrial environments.
- Termination:
- CAN Bus: Requires termination resistors at both ends of the bus to ensure signal integrity and reduce reflections.
- RS-485: Requires termination resistors at the two ends of the bus to prevent signal reflection, and the termination scheme may vary depending on the topology.
- Voltage Levels:
- CAN Bus: Uses differential signaling with voltage levels around 2.5 V when idle. This differential signaling contributes to its noise immunity.
- RS-485: Uses differential signaling with voltage levels that can vary but are typically in the range of -5 to +5 V or -3 to +3 V.
- Standardisation:
- CAN Bus: Governed by various standards, including ISO 11898, and is widely used in the automotive industry.
- RS-485: Governed by the RS-485 standard (TIA/EIA-485-A), which defines the electrical characteristics of the interface.
In summary, CAN Bus and RS-485 are both used for serial communication, but they differ in terms of network topology, communication speed, error handling, noise immunity, and other characteristics, making them suitable for different applications. The choice between them depends on the specific requirements of the system you’re designing.
The Controller Area Network (CAN) technology is a vital component of the modern automotive industry, enabling seamless and efficient communication between electronic control units (ECUs) within a vehicle. Its message-based protocol, noise immunity, error detection, and automatic re-transmission mechanisms make it a robust and reliable solution for the ever-increasing complexity of automotive systems. As technology continues to evolve, CAN Bus remains at the forefront, ready to drive innovation in the automotive world.
Benefits of Utilising CAN Bus
Reliability: Enhancing Error Handling and Data Transmission
The CAN bus system boasts remarkable reliability by streamlining error diagnosis and configuration across Electronic Control Units (ECUs). It features robust error-checking mechanisms and fault tolerance, ensuring precise data transmission, even in noisy surroundings. Notably, it maintains operational functionality in the face of node failures.
Cost-Effectiveness: Simplifying Connectivity
CAN bus technology presents a cost-effective solution through its efficient communication protocol for ECUs. By employing a single CAN interface, it simplifies wiring complexity and reduces the demand for intricate cable networks. This not only expedites installation but also minimises the risk of errors, saving valuable time and resources.
Efficiency: Prioritising Data Transmission
CAN messages are efficiently prioritised and employ bitwise arbitration via unique IDs. This prioritisation guarantees uninterrupted data flow for the highest-priority IDs, resulting in low-latency data transmission. This, in turn, significantly enhances system performance and safety, making it a preferred choice for various applications.
Flexibility: Adaptability and Scalability
Each ECU is equipped with a versatile chip capable of receiving all transmitted messages, assessing their relevance, and responding accordingly. This design offers exceptional flexibility, allowing for seamless modifications and the addition or removal of additional nodes as required. This adaptability is invaluable in accommodating evolving system needs.
Overview of Key CAN Bus Applications
Automotive Electronics: Elevating Vehicle Performance
CAN Bus technology finds extensive application in the automotive sector, spanning functions from engine control and instrument panels to safety systems and entertainment units. Its high-speed transmission and unwavering reliability foster real-time communication among a multitude of in-vehicle devices, ultimately enhancing both the driving experience and overall vehicle performance.
Industrial Automation: Boosting Production Efficiency
In the industrial automation landscape, CAN Bus serves as the connective tissue linking a diverse array of automated devices, including robots and production line monitoring systems. This real-time communication prowess enables these factory machines to collaborate effectively, leading to a substantial increase in production efficiency.
Aerospace: Enhancing Control and Reliability
CAN bus systems play a pivotal role in the aerospace industry, revolutionizing communication and control within spacecraft and unmanned aerial vehicles (UAVs). This technology elevates reliability and empowers real-time monitoring and control, which is paramount in the demanding aerospace environment.
Embedded Systems: Seamless Connectivity Across Industries
CAN Bus is a linchpin in the world of embedded systems, facilitating connections among a wide spectrum of devices, such as smart home systems, medical equipment, and consumer electronics. This seamless connectivity ensures efficient data exchange and device control, serving as the foundation for numerous innovative applications across various industries.